Выбор и обоснование схемы измельчения, классификации и обогащения руды
Зарегистрируйся в два клика и получи неограниченный доступ к материалам,а также
промокод
на новый заказ в Автор24. Это бесплатно.
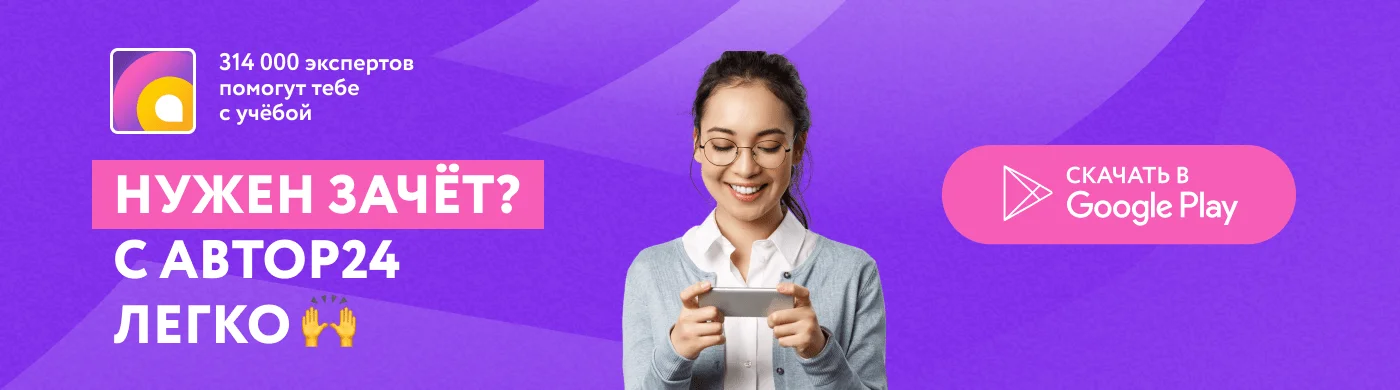
Основной метод обогащения апатитовых руд - флотация. Особенности флотационных свойств апатита связаны с ионным характером строения кристаллической решетки, что обусловливает активное взаимодействие его с реагентами-собирателями анионного типа с карбоксильной и сульфатной солидофильной группами [2].
Наилучшие условия для флотации карбоксильным собирателем создаются в щелочной среде в пределах pH = 9,0 - 9,5. При более высокой щелочности активируется флотация темноцветных минералов и снижается качество апатитового концентрата. На действующих обогатительных фабриках основной реагент-собиратель представляет собой омыленную смесь дистиллированного таллового масла, сырого таллового масла, технических жирных кислот, вторичного масла, вторичного масляного гудрона и окисленного петролатума. Соотношение отдельных компонентов реагентов-собирателей меняют в зависимости от свойств флотируемой руды, наиболее активны компоненты в виде натриевых мыл.
Избирательность флотации повышается при добавлении жидкого стекла, которое в определенных интервалах концентраций предпочтительнее адсорбируется на силикатных и кремнистых минералах, повышая гидратированность их поверхности и предотвращая взаимодействие с собирателем. Более избирательная флотация происходит и при добавлении реагентов из класса гидрофильных полимеров органического происхождения.
Большое влияние на режим флотации апатита оказывает степень измельчения руды. Лучше всего флотируются частицы средней крупности. Переизмельчение руды не только снижает качество концентрата, но и уменьшает производительность оборудования, увеличивает расход реагентов и потери апатита при сгущении и сушке. Поэтому очень важна оптимизация режима рудоподготовки перед флотацией.
На выбор схемы и режима обогащения, апатитовых руд большое влияние оказывают сопутствующие минералы. Наибольшую трудность представляет процесс отделения апатита от кальцита и доломита, гидрослюд и других вторичных минералов.
Присутствие в рудах, помимо апатита, других полезных минералов обусловливает необходимость усложнения технологических схем. В этом отношении технология обогащения выделенных типов апатитовых руд характеризуется определенной спецификой и даже существенными отличиями [3].
Технологические исследования по выявлению наиболее рациональной схемы переработки апатитовых руд на основе их комплексного использования проводятся на всех стадиях поисково-разведочного процесса, но с различными целевыми установками, детальностью и с применением разных способов и методов. На стадии поисковой оценки важно установить степень соответствия вещественного состава и технологических свойств руд нового объекта и руд, промышленно освоенных месторождений методом аналогии, для чего выделяются природные типы сырья (по составу, структурно-текстурным характеристикам, физико-механическим свойствам, агрегатному состоянию, химическому составу рудообразующих минералов), т.е. по тем параметрам, по которым проводится аналогия. В ограниченном объеме (по единичным пробам или рудным пересечениям) на материале малообъемных проб для каждого выделенного типа или сорта проводятся опыты по разделению минералов.
Три обогатительные фабрики ПО «Апатит» - АНОФ - (1-3) перерабатывают руды, поступающие из пяти разрабатываемых месторождении, поэтому их минеральный состав, а следовательно, и технологические свойства нс остаются постоянными
Зарегистрируйся, чтобы продолжить изучение работы
. Добытая руда обогащается по общей технологической схеме, основу которой составляют трехстадийное дробление, измельчение с предварительной классификацией материала, флотация апатита, обезвоживание и сушка концентрата. На флотацию поступает руда, содержащая 52-55% класса крупности - 0,074 мм. Схема включает основную и контрольную флотации и три перечистки концентрата (рис. 2.1). В качестве собирателя используется омыленная смесь из дистиллированного и сырого талловых масел, вторичного масляного гудрона, окисленного петролатума и технических жирных кислот; для депрессии нефелина, полевых шпатов, сфена, эгирина и титано-магнетита применяется жидкое стекло, а регулятором флотации является ОП-4 и каустическая сода.
Апатитовый концентрат содержит не менее 39,4% Р2О5, крупность не превышает 11,5% класса +0,16 мм, влажность не более 1% (ГОСТ 5.1182-72).
За более чем 50-летний период технологического изучения и промышленного освоения хибинских месторождении накоплен большой опыт технологии обогащения апатито-нефелиновых руд в лабораторном, опытно-промышленном и в производственном масштабах. Лабораторные и опытно-промышленные испытания выполнялись институтами Механобр, ГИГХС, Горным институтом Кольского филиала АН СССР и Центральной лабораторией производственного объединения «Апатит» на материале более 250 проб массой от 0,5 т до нескольких сотен тонн. По составу руды представлены балансовыми и забалансовыми, отдельными природными (текстурными) типами и их смесями в разных сочетаниях, неизмененными и подвергнутыми вторичным процессам (шпреуштейнизации), а также разубоженными вмещающими породами.
По месту отбора исследованные пробы охватывают как эксплуатируемые, так и новые месторождения, каждое из рудных тел в контурах открытой и подземной отработки.
В процессе испытаний изучены минеральный и химический состав исходного материала проб; физико-химические, гравитационные и флотационные свойства минералов; состав, строение и дефекты их кристаллических решеток, наличие изоморфных примесей; параметры технологических процессов; возможные варианты технологических схем; различные методы обогащения и типы флотационных реагентов [4].
Рисунок 2.1 - Технологическая схема получения апатитового концентрата на обогатительной фабрике (АНОФ-3)
АНОФ-1
Одна из старейших отечественных фабрик для обогащения несульфидных руд. Она введена в эксплуатацию в 30-е годы и в дальнейшем неоднократно расширялась и модернизировалась.
Фабрика перерабатывает руды с содержанием 10,5-17,0% Р2О3. Руда подается в думпкарах грузоподъемностью 90 т.
Дробление руды производится в три стадии с помощью конусных дробилок крупного, среднего и мелкого дробления с промежуточным грохочением. Крупное дробление осуществляется ККД-900, среднее - КСД-2200, мелкое - КМД-2200.
Первая стадия грохочения производится с помощью колосникового грохота, вторая и третья стадии - с помощью инерционных грохотов.
Дробленая руда содержит 4% класса +25 мм; 31% класса - 25 +14 мм и 62% класса -10 мм (в том числе 4-6% класса - 0,01 мм).
Измельчение осуществляется на трех отдельных секциях до крупности измельчения 33-36% класса - 0,074 мм.
Флотация руды на двух потоках производится без доизмельчения концентрата
50% курсовой работы недоступно для прочтения
Закажи написание курсовой работы по выбранной теме всего за пару кликов. Персональная работа в кратчайшее время!